Pulse Jet Dust Collectors in the Rubber and Plastics Industry: Controlling Odor and Dust Emissions
- Share
- publisher
- Peter
- Issue Time
- Feb 21,2025
Summary
Highlights pulse jet dust collectors' role in rubber/plastics—controlling dust, removing harmful gases/odors. Urges investment for worker safety, compliance, and equipment protection.
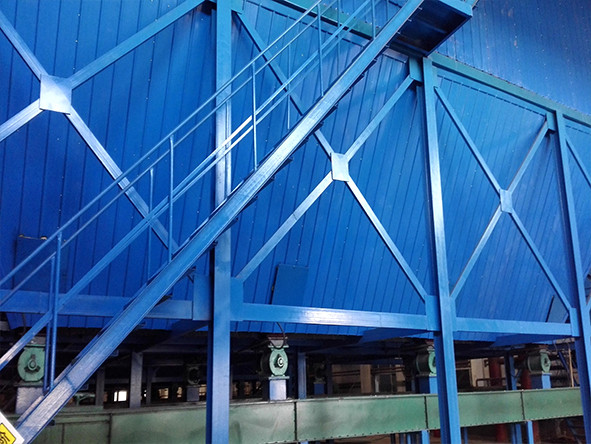
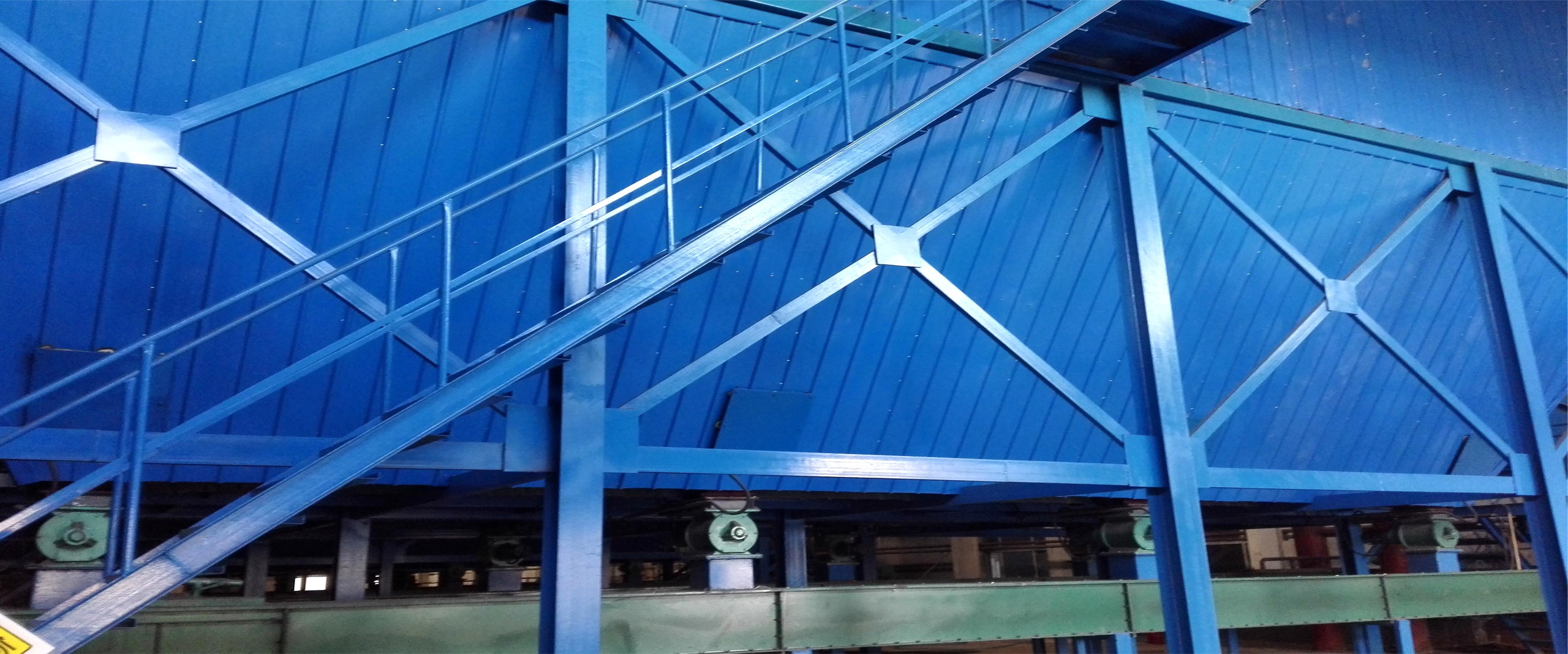
The rubber and plastics industries are essential to numerous sectors, from automotive manufacturing to packaging. However, with production processes involving high temperatures, chemicals, and mechanical work, these industries face significant challenges with airborne dust and odors. As manufacturing continues to evolve, addressing these issues effectively has become crucial not only for improving worker health and safety but also for maintaining operational efficiency. This is where pulse jet dust collectors come into play, offering a powerful solution to both dust and odor emissions while ensuring cleaner air in the workplace.
Common Challenges in the Rubber and Plastics Industry
1. Dust Pollution and Health Risks: The production of rubber and plastics often involves processes like grinding, molding, and extrusion, all of which generate significant amounts of fine dust particles. Exposure to these particles, particularly from rubber and plastic materials, can lead to long-term respiratory issues, skin irritations, and other health concerns for workers. Silica dust and plastic particles are especially harmful, posing risks like chronic lung disease.
2. Odor Emissions: In addition to dust, the chemical processes used in rubber and plastics production—such as vulcanization or mixing—release strong and unpleasant odors. Many of these odors come from volatile organic compounds (VOCs) and other harmful gases that can compromise air quality, affect worker well-being, and violate environmental regulations.
3. Equipment Contamination and Downtime: Dust buildup can cause machinery to malfunction, resulting in frequent repairs, lower production speeds, and costly downtime. A clean environment is not only essential for worker safety but also for machine efficiency.
4. Regulatory Compliance and Environmental Impact: As environmental regulations become more stringent, industries are expected to meet strict air quality standards. Failure to do so can result in fines, reputational damage, and even the shutdown of operations. Therefore, controlling emissions, both in terms of dust and odor, is more critical than ever.
How Pulse Jet Dust Collectors Provide a Solution
Pulse jet dust collectors, also known as industrial air filtration systems or baghouse dust collectors, are designed to effectively capture fine dust particles while ensuring minimal disruption to the production process. These systems use a pulse of compressed air to periodically clean the filters, ensuring that they maintain their efficiency over time. Here’s how these dust collectors help address the challenges faced by the rubber and plastics industry:
1. Efficient Dust Removal and Worker Health Protection
The primary function of pulse jet dust collectors is to capture airborne dust, preventing it from circulating in the air and ensuring a cleaner environment for workers. By removing harmful particles from the air, these dust collectors significantly reduce the risks of respiratory issues caused by prolonged exposure to rubber and plastic dust.
A plastic manufacturing company in the U.S. installed a pulse jet dust collection system and reported a 50% reduction in respiratory-related health complaints among workers within just three months. This improvement resulted in fewer sick days, lower healthcare costs, and enhanced employee productivity.
2. Odor and Gas Removal: Enhancing Air Quality
Many rubber and plastics production processes release harmful gases and odors, such as VOCs from chemicals and plasticizers. Pulse jet dust collectors can be equipped with activated carbon filters or other specialized filtration media to capture these gases and neutralize odors. This ensures that the air in the workplace remains clean and safe, promoting better air quality and reducing employee discomfort.
For example, a rubber production plant in Germany faced strong chemical odors from the vulcanization process. After installing a pulse jet dust collection system with odor control capabilities, the plant achieved a 70% reduction in odors, resulting in better worker satisfaction and a healthier working environment.
3. Preventing Equipment Damage and Reducing Downtime
By capturing dust before it settles on machines, pulse jet dust collectors help prevent contamination that can clog filters, damage sensitive components, and cause mechanical breakdowns. This leads to smoother operations, reduced maintenance costs, and a more reliable production process.
A leading rubber manufacturer in India found that after implementing a pulse jet dust collection system, they experienced a 25% reduction in machine maintenance costs, as dust no longer accumulated on production equipment. This allowed them to increase production rates and reduce downtime, ultimately improving profitability.
4. Regulatory Compliance and Sustainability
As regulations around air quality become stricter, industries must ensure that they meet environmental standards for both dust and odor emissions. Pulse jet dust collectors help businesses stay compliant by capturing particulate matter and neutralizing harmful gases. These systems also contribute to more sustainable manufacturing by reducing waste and minimizing the environmental footprint of operations.
For instance, a plastics processing company in China installed a pulse jet dust collector system to comply with new air quality standards. They reported a 50% decrease in airborne pollutants and avoided potential fines, showcasing their commitment to sustainability and environmental responsibility.
Real-World Success: Case Study in the Rubber Industry
Take the example of XYZ Rubber Co., a company based in Brazil that manufactures rubber parts for the automotive industry. Before installing a pulse jet dust collection system, XYZ Rubber Co. faced significant challenges with dust accumulation and chemical odors, leading to poor air quality, frequent machine breakdowns, and health complaints from employees.
After upgrading to an advanced pulse jet dust collection system, XYZ Rubber Co. achieved:
A 90% reduction in airborne dust levels, significantly improving worker health and morale.
Increased equipment efficiency, with a 30% reduction in downtime due to fewer machine malfunctions.
A cleaner and more compliant factory, meeting strict environmental regulations and improving their sustainability efforts.
As a result, the company experienced improved productivity, better employee retention, and higher customer satisfaction.
The Future of Dust Collection in Rubber and Plastics
As the rubber and plastics industries continue to grow, the need for efficient and environmentally friendly dust collection systems will only increase. Future advancements in filtration technology, including the integration of IoT, AI, and smart sensors, will allow companies to optimize dust collection, reduce energy consumption, and maintain a cleaner, safer working environment.
Call to Action: Create a Cleaner, Safer, and More Efficient Production Environment
If your rubber or plastics manufacturing facility is struggling with dust and odor control, it’s time to invest in a pulse jet dust collector. These systems will improve air quality, protect your workers, reduce downtime, and ensure compliance with environmental regulations.
Ready to enhance your operations? Contact us today to learn how our pulse jet dust collectors can help you create a cleaner, safer, and more efficient production environment. Don’t wait—take the first step toward better health, sustainability, and productivity today!